Unlocking the Potential of PC ABS in 3D Printing
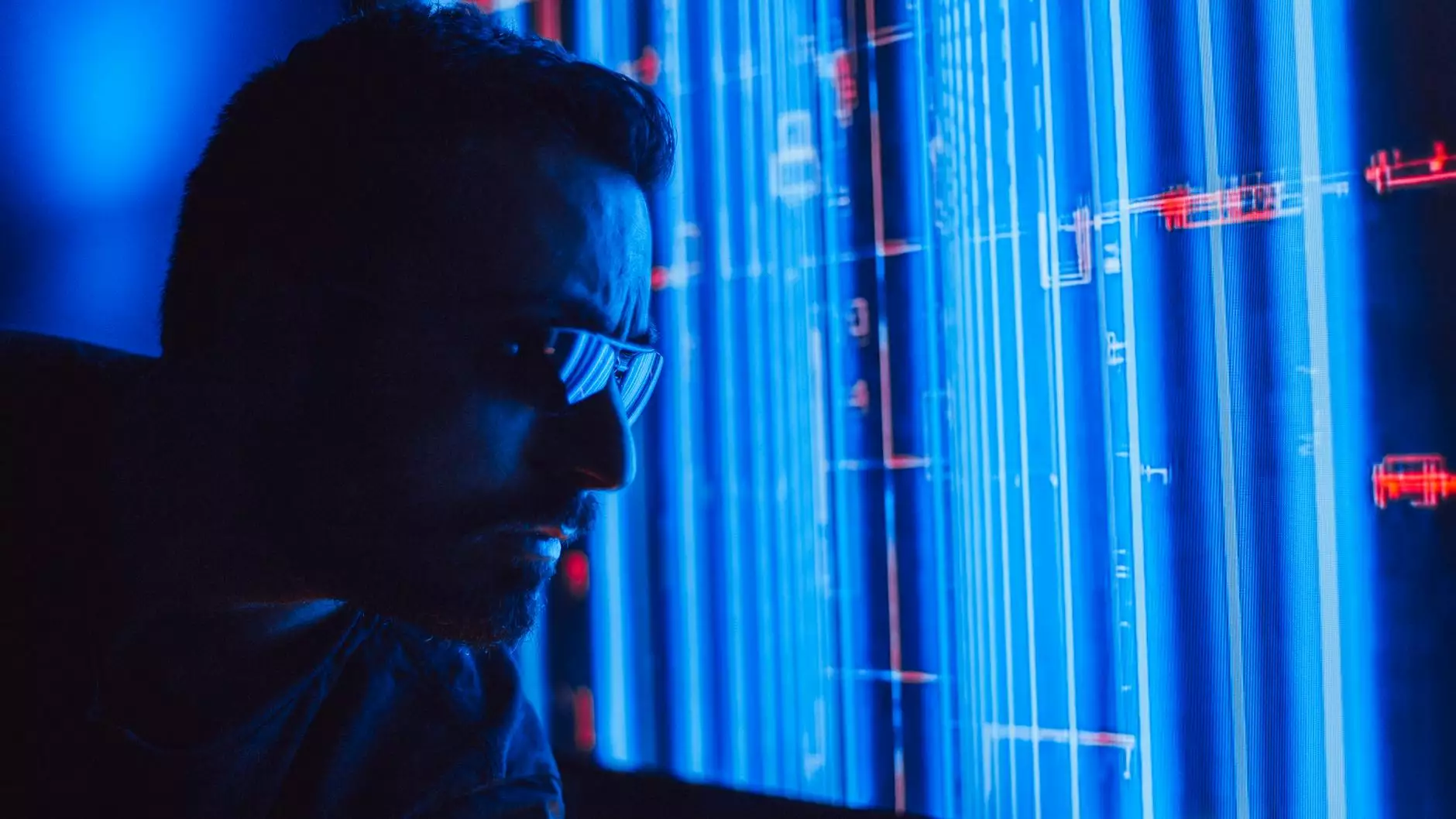
In today's fast-paced world, businesses are constantly on the lookout for innovative materials to streamline their production processes. One such material that has gained significant attention in the realm of 3D printing is PC ABS. This remarkable alloy, composed of polycarbonate (PC) and acrylonitrile-butadiene-styrene (ABS), offers a unique blend of strength, flexibility, and durability, making it a preferred choice for various applications.
What is PC ABS?
PC ABS is a thermoplastic polymer blend that combines the best properties of its parent materials, polycarbonate and ABS. Polycarbonate is known for its exceptional impact resistance and optical clarity, while ABS brings advantages such as easier processing and a lower cost. When combined, PC ABS offers a material that is not only tough but also versatile, making it ideal for a diverse range of industries.
The Composition of PC ABS
- Polycarbonate: Contributes strength and heat resistance.
- ABS: Provides impact resistance and improved manufacturability.
- Blend Properties: The combination results in a material that balances rigidity and toughness.
Advantages of Using PC ABS in 3D Printing
The incorporation of PC ABS in 3D printing offers several distinct advantages:
1. Enhanced Durability
One of the primary benefits of using PC ABS is its enhanced durability. This material demonstrates a high resistance to impact, which is particularly crucial for parts that need to withstand mechanical stress. This makes it an excellent choice for functional prototypes and end-use components.
2. Excellent Heat Resistance
PC ABS can endure high temperatures without losing its structural integrity. This property is vital for applications that involve exposure to heat, such as automotive components and electronic housings.
3. Versatile Applications
Due to its unique combination of properties, PC ABS can be employed in a wide array of applications, including:
- Automotive parts (dashboard components, housings)
- Consumer electronics (enclosures, switches)
- Aerospace (interior parts)
- Medical devices (casing, instrumentation)
4. Improved Aesthetic Qualities
Another notable advantage is the aesthetic quality of PC ABS. This material can be finished in various ways, offering smooth surfaces and the ability to be easily painted or coated. This is particularly beneficial for consumer-facing products that require a polished appearance.
Applications of PC ABS in Business
The versatility of PC ABS allows it to fit into numerous business sectors. Here are some notable applications:
1. Automotive Industry
In the automotive sector, where parts are often exposed to harsh environmental conditions, PC ABS finds its way into dashboard assemblies and HVAC components. With the ability to withstand high temperatures and physical wear, it ensures longevity and reliability.
2. Consumer Electronics
The consumer electronics industry leverages the properties of PC ABS to create durable yet lightweight casing for devices such as smartphones and laptops. The material’s ability to be molded into intricate designs also aids in producing aesthetically pleasing products.
3. Aerospace Components
Durability and lightweight characteristics are a priority in aerospace applications. PC ABS is ideal for interior components where weight savings can lead to improved fuel efficiency.
3D Printing with PC ABS: Best Practices
For businesses interested in utilizing PC ABS in their 3D printing processes, there are several best practices to follow:
1. Printer Settings
When printing with PC ABS, it's crucial to adjust the printer settings for optimal results. Recommended settings include:
- Temperature: Print at a nozzle temperature between 240°C to 260°C.
- Build Plate: Use a heated bed set to around 80°C to prevent warping.
2. Adequate Ventilation
As with many thermoplastics, PC ABS can emit fumes during printing. Ensure that your workspace is well-ventilated to ensure safety and comfort while printing.
3. Post-Processing Techniques
To achieve the best surface finish and aesthetic appeal, consider post-processing methods such as sanding and painting. This can significantly enhance the final product's look.
Challenges of PC ABS in 3D Printing
While there are numerous benefits to using PC ABS, some challenges may arise:
1. Warping
Due to its thermal properties, PC ABS is prone to warping during the cooling phase. To combat this, ensure a controlled environment and use a heated bed during printing.
2. Layer Adhesion
Ensuring strong layer adhesion can be a challenge with PC ABS. Adjusting printing temperatures and speeds may aid in improving the adhesion quality.
Future Prospects of PC ABS in the Industry
As technology continues to evolve, the future of PC ABS in 3D printing looks promising. With continuous advancements in material science, it is expected that new formulations will emerge, potentially enhancing properties such as strength, flexibility, and processing ease. Additionally, the growing trend of sustainable materials may lead to the development of more eco-friendly versions of PC ABS.
Conclusion: Embracing PC ABS for Business Growth
In conclusion, the integration of PC ABS in 3D printing opens new doors for businesses looking to innovate and improve their production lines. From automotive to consumer electronics, this versatile material provides a mix of durability and aesthetic appeal that can significantly enhance product offerings.
For businesses aiming to leverage the benefits of PC ABS, the key lies in understanding its properties, optimizing 3D printing techniques, and staying ahead of industry trends. By embracing this material, companies can not only drive efficiency and savings but also position themselves as leaders in the competitive landscape.
At Infotron, we help businesses like yours navigate the exciting world of 3D printing with materials like PC ABS. Contact us today to learn how we can support your projects and enhance your productivity.