Understanding Prestressed Metal Bellows: A Key Component in Modern Engineering
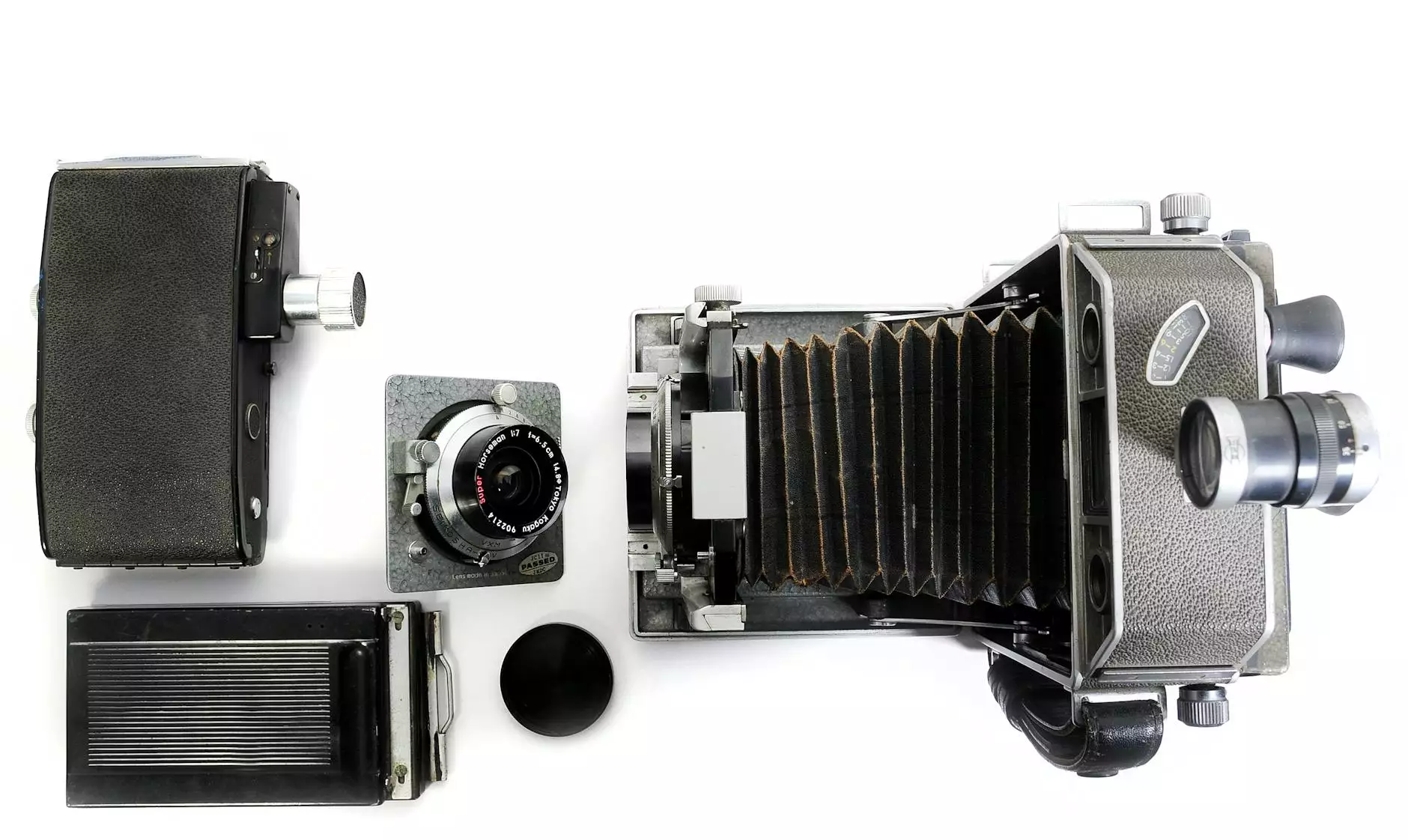
Prestressed metal bellows represent a critical innovation in engineering design, offering unique solutions for pressure and thermal management across various applications. This article delves deep into what prestressed metal bellows are, their manufacturing processes, applications across industries, and their undeniable advantages. Understanding these components is essential for professionals in fields such as manufacturing, aerospace, and even the automotive industry.
What Are Prestressed Metal Bellows?
Prestressed metal bellows are engineered components that are designed to absorb motion, pressure, and thermal expansions in mechanical systems. Unlike traditional bellows, which are typically used in less demanding applications, prestressed metal bellows are created using advanced manufacturing processes that enhance their strength and durability.
Construction and Design Features
The design of prestressed metal bellows involves several key features:
- Material Selection: Typically made from stainless steel or other high-strength alloys that offer excellent corrosion resistance and mechanical properties.
- Prestressing Process: The process involves applying forces to the bellows to enhance their load-bearing capacity. This preloading reduces the risk of fatigue failure under cyclic loading.
- Geometric Configurations: Available in various shapes and sizes, the geometry of the bellows can be customized to meet the specific requirements of an application.
The Manufacturing Process of Prestressed Metal Bellows
Step 1: Designing the Bellows
The first step in producing prestressed metal bellows is careful design, utilizing computer-aided design (CAD) software. This allows engineers to simulate performance under varying loads and pressure conditions.
Step 2: Forming the Bellows
After design, the manufacturing process begins with the forming of the bellows. Techniques like deep drawing or hydroforming can be employed to achieve the desired shape and thickness while ensuring consistency across pieces.
Step 3: Prestressing the Bellows
Once formed, the bellows undergo the prestressing process. This involves applying controlled forces that compress the material, enhancing its fatigue resistance and overall durability.
Step 4: Testing and Quality Control
Quality assurance is paramount. Each batch of prestressed metal bellows is subjected to rigorous testing to ensure it meets industry standards. Tests may include pressure testing, thermal cycling, and dimensional verification.
Applications of Prestressed Metal Bellows
Prestressed metal bellows find applications across numerous industries due to their versatile nature. Here, we explore some of the most significant uses:
1. Aerospace Industry
In the aerospace sector, prestressed metal bellows are essential for managing the complex thermal and pressure conditions that aircraft and spacecraft encounter. They are commonly found in:
- Engine exhaust systems
- Fuel systems
- Thermal expansion joints
2. Automotive Industry
The automotive industry benefits significantly from the use of prestressed metal bellows in applications such as:
- Exhaust systems to mitigate vibrations
- Turbochargers for improved engine efficiency
- Suspension systems for enhanced vehicle stability
3. Oil and Gas Sector
In oil and gas exploration and production, these bellows are employed to accommodate thermal expansion and contractions, ensuring pipeline integrity. Their use extends to:
- Pressure containment systems
- Flow control applications
- Safety valve assemblies
4. HVAC Systems
Heating, ventilation, and air conditioning (HVAC) systems leverage prestressed metal bellows to handle fluctuations in pressure and temperature, ensuring efficient operation and performance.
Advantages of Using Prestressed Metal Bellows
The adoption of prestressed metal bellows brings numerous advantages:
- Enhanced Durability: The prestressing process significantly increases the component's lifespan, making them suitable for demanding applications.
- Vibration Isolation: They effectively isolate vibrations, crucial in many high-performance systems.
- Pressure Management: Bellows can handle high-pressure environments safely, preventing leaks and failures.
- Versatility: Suitable for a wide range of industries and adaptable to various design specifications.
Future Trends in Prestressed Metal Bellows Technology
As industries evolve, the demand for more efficient and reliable components increases. The future of prestressed metal bellows will likely focus on:
- Advanced Materials: The development of lighter and stronger materials to further enhance performance.
- Smart Technology: Integration of sensors to monitor the health of the bellows in real-time.
- 3D Printing: The use of additive manufacturing techniques to customize and produce bellows more efficiently.
Conclusion
In conclusion, prestressed metal bellows are not only crucial components in various industrial applications but are also a symbol of modern engineering excellence. Their ability to withstand extreme conditions while providing flexibility and durability makes them a preferred choice for engineers across the globe. With ongoing advancements in materials and manufacturing technologies, the future of these components shines brightly, promising even greater innovations that will continue to drive efficiency and performance across industries.
For those interested in acquiring high-quality prestressed metal bellows, look no further than ovictorgroup.com, where engineering meets excellence in manufacturing.