CNC Lathe Machining Parts: Transforming the Future of Manufacturing
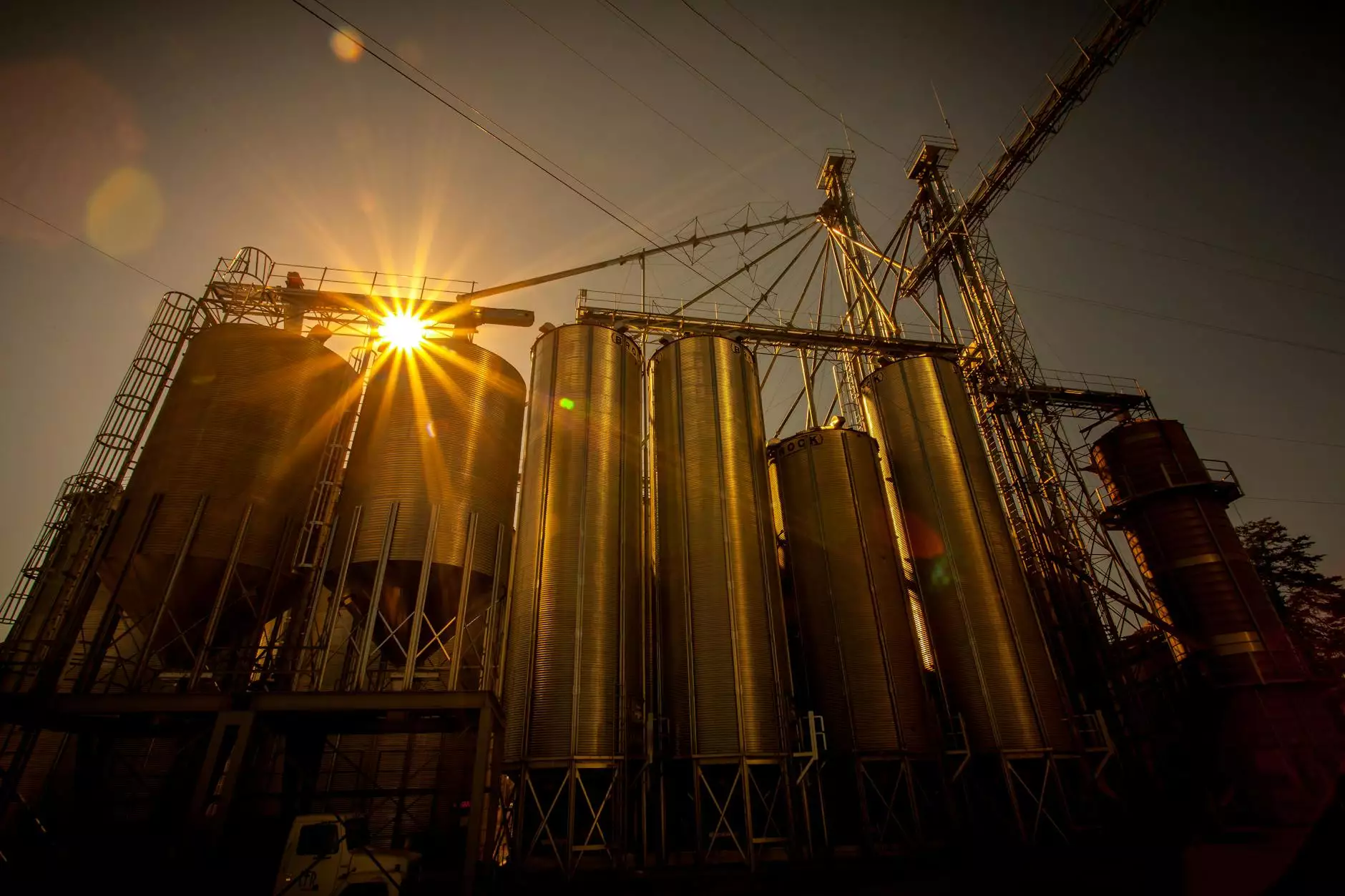
In today’s booming manufacturing industry, precision and efficiency are paramount. CNC lathe machining parts have emerged as a key solution for businesses seeking to enhance their production capabilities. This article delves into the significance of CNC lathe machining, the processes involved, and how companies like DeepMould.net play a pivotal role in this arena.
Understanding CNC Lathe Machining
CNC stands for Computer Numerical Control, which is a method used in manufacturing where computers control machine tools. Lathe machining is one of the oldest methods of manufacturing, where a block of material is rotated while a cutting tool shapes it. Together, CNC lathe machining combines traditional methods with advanced technology to produce components with exceptional precision.
The Process of CNC Lathe Machining
The CNC lathe machining process involves several carefully orchestrated steps:
- Design: Engineers create a 3D model of the part using CAD software.
- Programming: The CNC machine is programmed based on the specifications detailed in the CAD design.
- Setup: The raw material is secured in the lathe, and the appropriate tools are selected.
- Machining: The CNC machine begins the cutting process, shaping the material according to the programmed instructions.
- Quality Control: After machining, the part undergoes a thorough inspection to ensure it meets all specifications.
Types of CNC Lathe Machining Parts
There are numerous parts that can be produced via CNC lathe machining. Some of the most common include:
- Shafts: Used in various machinery, shaft components require high precision and strength.
- Bushings: These components are often used to reduce friction in machinery.
- Housings: Essential for enclosing other mechanical components and ensuring durability.
- Fittings: Used in piping and fittings, these parts often require intricate designs and tight tolerances.
- Custom Parts: Businesses often require unique components tailored to specific applications, which CNC machining fulfills effectively.
Why Choose CNC Lathe Machining Parts?
Several advantages make CNC lathe machining parts a preferred choice for manufacturers:
- Precision: CNC machining provides unparalleled accuracy, which is essential for complex parts that require tight tolerances.
- Consistency: Machines produce uniform parts over large batches, ensuring quality across all products.
- Flexibility: CNC machines can easily switch between different part designs with minimal downtime due to programming modifications.
- Efficiency: High-speed machining reduces production time, enabling manufacturers to meet tight deadlines.
- Reduced Waste: Advanced error-checking in programming minimizes material waste, leading to cost savings.
Applications of CNC Lathe Machining Parts
CNC lathe machining parts are integral to various industries. Here are some of the primary sectors benefiting from this technology:
Aerospace
The aerospace industry demands parts with extreme durability and precision, making CNC lathe machining essential for creating components such as engine housings and landing gear parts.
Automotive
In the automotive sector, custom parts like drive shafts and brake components are frequently manufactured using CNC lathe machining due to the need for precision and reliability.
Medical
Medical equipment and devices often require highly specialized components that must adhere to strict regulations. CNC machining provides the necessary precision for manufacturing parts like surgical tools and implants.
Electronics
The electronics sector relies on CNC lathe machining for producing small, intricate parts such as connectors and circuit board housings.
Quality Assurance in CNC Machining
Quality assurance is a fundamental aspect of CNC machining at companies like DeepMould.net. Rigorous testing and adherence to industry standards ensure that every part produced meets client expectations and regulatory requirements.
Inspection Techniques
To maintain high-quality standards, several inspection techniques are employed:
- CMM (Coordinate Measuring Machine): Used to measure the physical geometrical characteristics of a part.
- Visual Inspection: Involves checking the surface quality and dimensions with naked eyes or magnifying tools.
- Functional Testing: Ensures that parts perform as intended in real-world applications.
Choosing the Right CNC Machining Partner
Finding the right CNC machining partner can significantly affect the quality and speed of production. Here are critical factors to consider when evaluating a potential supplier:
Experience and Expertise
Look for companies with significant experience in CNC lathe machining. DeepMould.net, for instance, has a proven track record of delivering high-quality parts across various industries.
Technology and Equipment
Advanced machinery is essential for precision. A reliable partner must utilize updated equipment and methodologies.
Customization and Flexibility
The ability to customize parts according to unique specifications is vital. Ensure that the supplier can work with you to develop tailored solutions.
Customer Support and Communication
Efficient communication and support during the entire process are crucial. A responsive partner can help resolve any issues that may arise.
Future Trends in CNC Lathe Machining
The CNC machining industry is continually evolving. Some trends shaping its future include:
- Automation: Increased automation is leading to faster production rates and improved efficiency.
- Advanced Materials: The use of new materials, including composites and lightweight alloys, is expanding CNC machining possibilities.
- IoT Integration: The Internet of Things is enabling real-time monitoring of machining processes, fostering improved performance.
- Sustainability: A focus on sustainable practices is driving developments in machining techniques and materials.
Conclusion
In summary, CNC lathe machining parts represent a significant advancement in manufacturing technology, providing unparalleled precision, efficiency, and flexibility. As industries continue to rely on high-quality components, companies like DeepMould.net are leading the way in delivering innovative machining solutions. Embracing CNC machining technology not only enhances production capabilities but also places businesses at the forefront of their respective markets.
Investing in CNC lathe machining parts is not merely a decision for immediate needs; it is a strategic move towards future growth and adaptability in an ever-evolving manufacturing landscape.