Understanding and Utilizing Silicone Membrane Sheets in Various Applications
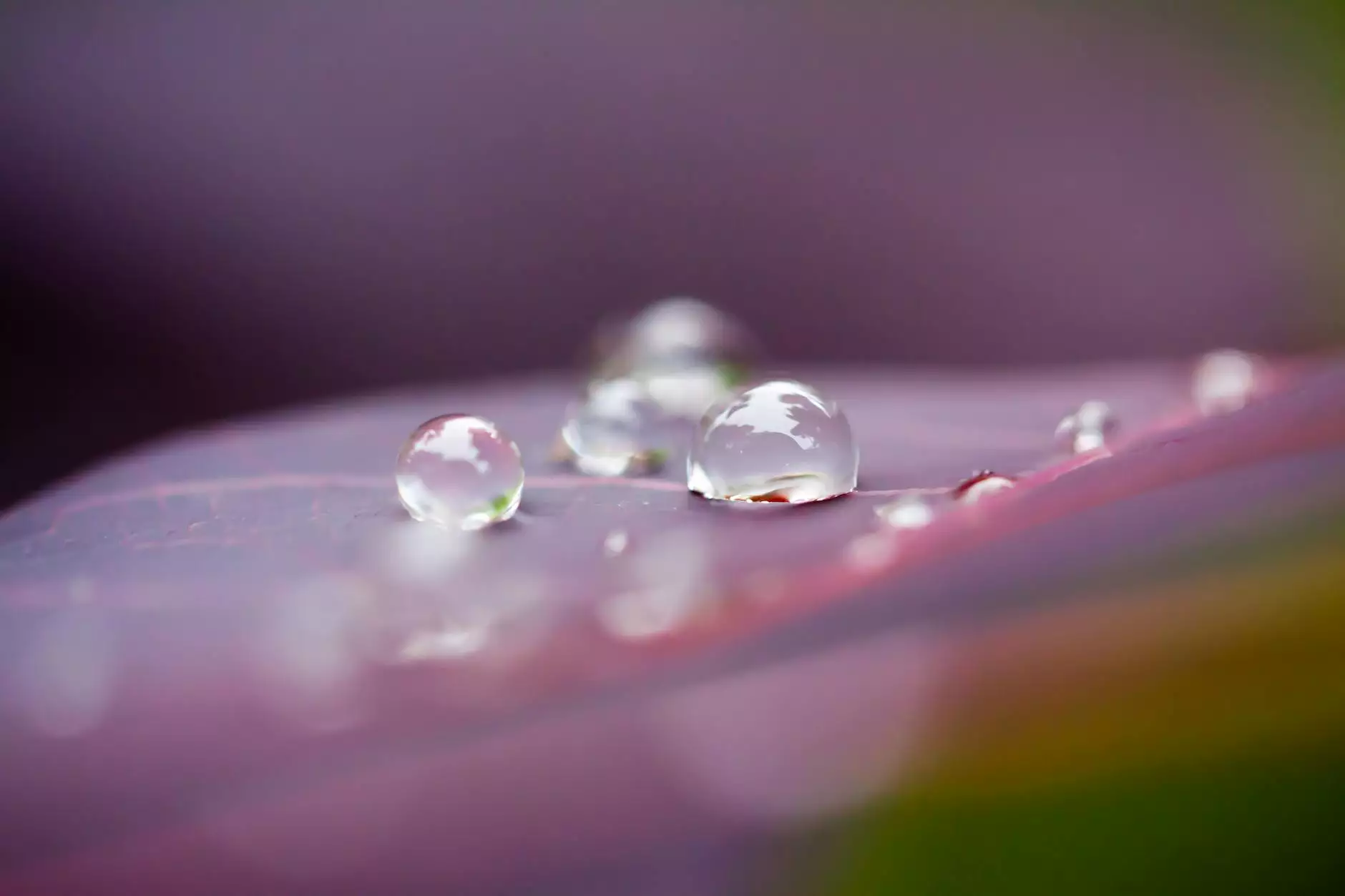
The world of modern business and manufacturing is continually evolving, introducing innovative materials that enhance efficiency and productivity. Among these, the silicone membrane sheet stands out due to its versatility, durability, and unmatched performance characteristics. This article will delve deep into the various aspects of silicone membrane sheets, their benefits, applications, and how they compare to other materials.
What is a Silicone Membrane Sheet?
A silicone membrane sheet is a flexible and durable layer made from silicone rubber, designed to be used in various industrial and commercial applications. Silicone is known for its excellent temperature resistance, chemical stability, and mechanical strength. These properties make silicone membranes ideal for vacuum forming, press molding, and other manufacturing processes.
The Advantages of Silicone Membrane Sheets
Utilizing silicone membrane sheets offers a range of benefits that make them a preferred choice in numerous industries:
- Durability: Silicone membranes are resistant to wear and tear, ensuring a long lifespan in demanding environments.
- Temperature Resistance: They can withstand a wide temperature range, typically from -60°C to +200°C, making them suitable for high-temperature applications.
- Chemical Resistance: Silicone is inert to many chemicals, which is essential for processes involving corrosive substances.
- Flexibility: The elastic nature of silicone allows these membranes to conform to various shapes and surfaces.
- Non-toxic and Biocompatible: They are safe for use in food and medical applications, ensuring compliance with health and safety standards.
Applications of Silicone Membrane Sheets
Silicone membrane sheets are employed in a myriad of applications across different sectors. Here are some of the prominent uses:
1. Vacuum Forming
In the vacuum forming process, heat is used to soften a plastic sheet, which is then shaped over a mold. Silicone membrane sheets create a perfect seal, contributing to the quality of the final product. Their flexibility and strength allow them to manage the varying pressures encountered during this process.
2. Medical Devices
In the medical field, silicone membranes are used in devices that require high levels of sterility and biocompatibility. They serve as seals and membranes in various medical machinery, ensuring safe and efficient operations.
3. Electronics
Silicone membranes are also critical in the manufacture of electronic devices, where they protect sensitive components from dust and moisture while allowing functionality. Their insulating properties contribute to enhanced device performance and longevity.
4. Automotive Industry
In the automotive sector, silicone membrane sheets are utilized in gaskets, seals, and other components that require durability and resistance to environmental factors. Their resilience to extreme temperatures and exposure to various chemicals is essential in ensuring vehicle longevity.
5. Food Processing
Due to their non-toxic nature, silicone membranes are widely used in food processing and packaging. They prevent contamination while maintaining the integrity of food products. Their ability to withstand high temperatures also makes them ideal for cooking applications.
Comparing Silicone Membrane Sheets with Other Membrane Types
When considering membrane options for various applications, it's essential to understand how silicone membrane sheets compare with other types, such as rubber membranes and natural rubber membranes:
Silicone vs. Rubber Membranes
While both silicone and rubber membranes serve similar purposes, silicone has superior performance characteristics in terms of temperature resistance and chemical stability. Rubber membranes can degrade when exposed to harsh chemicals or high temperatures, while silicone membranes maintain their integrity under such conditions.
Silicone vs. Natural Rubber Membranes
Natural rubber membranes can offer excellent elasticity and resilience, but they may not withstand extreme temperatures or harsh chemicals as well as silicone membranes. For applications requiring durability under challenging conditions, silicone membranes are the preferable choice.
Choosing the Right Silicone Membrane Sheet
When selecting a silicone membrane sheet for your business needs, consider the following factors:
- Thickness: Determine the required thickness based on the specific application. Thicker sheets provide added durability but may reduce flexibility.
- Durometer Rating: This scale measures the hardness of the silicone. Choose a softer sheet for applications requiring more flexibility.
- Temperature Range: Ensure the selected membrane can handle the maximum and minimum temperatures it will encounter in use.
- Chemical Compatibility: Assess the types of chemicals the membrane will be exposed to and ensure compatibility.
Conclusion
In conclusion, silicone membrane sheets represent a vital component in modern manufacturing and industrial processes. Their unparalleled durability, resistance to environmental factors, and versatility across multiple applications make them an essential material for many businesses. Whether you are engaging in vacuum forming, electronic manufacturing, or food processing, these silicone sheets provide the reliability and performance needed to enhance your operations.
As you explore options for purchasing silicone membranes, consider visiting vacuum-presses.com, where you can find a wide range of membranes, including options tailored to meet your specific business needs. Investing in high-quality silicone membrane sheets can lead to significant long-term benefits, ensuring your operations remain competitive and efficient.